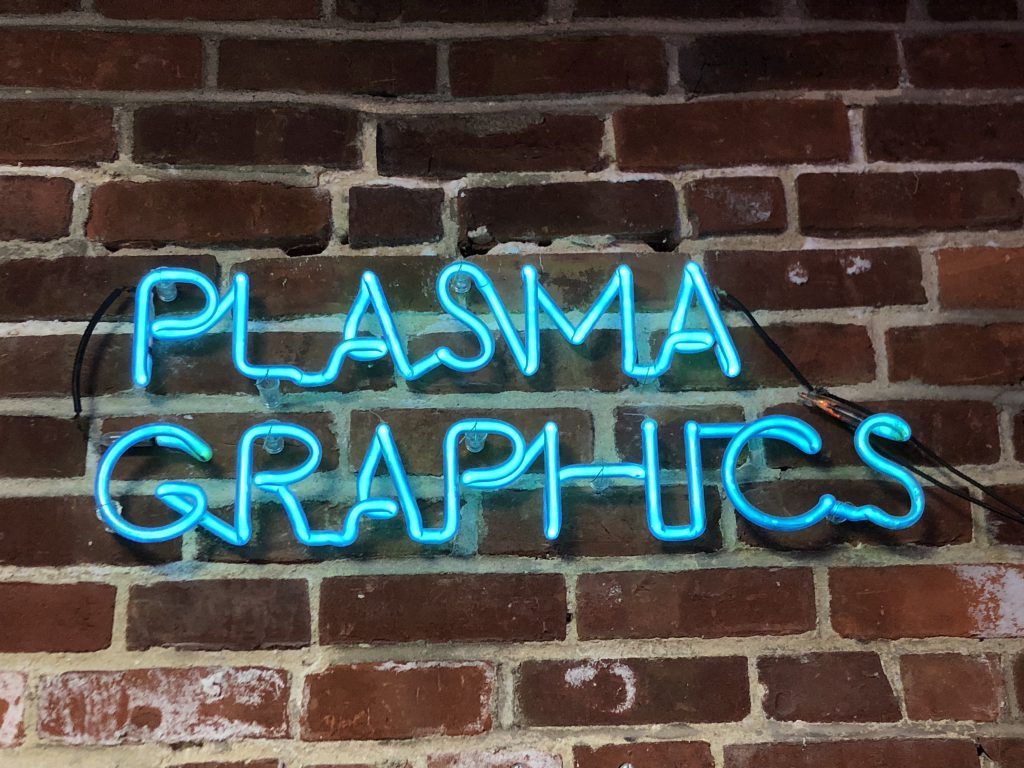
The last weekend of March, I had the opportunity to attend a workshop at Plasma Graphics in Atlantic City. Owner Tom Beibel and his son Steve (pictured below) hosted the workshop in their studio. I first visited Plasma Graphics back in 1997, when they hosted an afterparty for neon tubebenders at the Sign Expo trade show, so it was great to be back after such a long time.
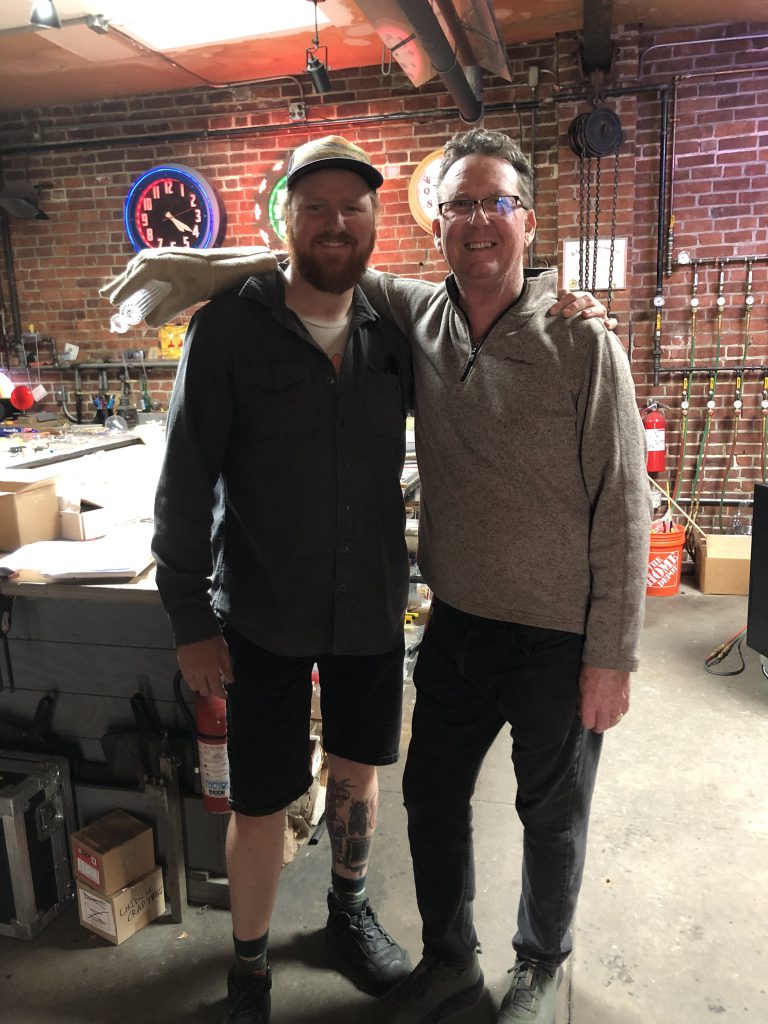
The class, which was described as a “plasma workshop” was taught by Miles Henry, glass artist and owner of Wildfire Studios in North Carolina. So, what is Plasma exactly? You’ve probably heard the word before when referencing blood, but in this case, we’re talking about plasma as it’s known to be the fourth state of matter. Or as the Princeton Plasma Physics Laboratory defines it:
Plasma is a state of matter along with solids, liquids and gases. When a neutral gas is heated such that some of the electrons are freed from the atoms or molecules, it changes state and becomes a plasma. It consists of a partially-ionized gas, containing ions, electrons, and neutral atoms. Neon signs and lightning are examples of plasma.
Even though I have been making neon signs since the early 1990s, I haven’t delved too much into the wonderful world of plasma except for a couple of similar workshops I took about 20 years ago, so this was an exciting opportunity for me to learn some new things about working with blown glass and the other noble gases. A very basic explanation of what we did during this workshop would be to say that we created pieces out of blown glass, and experimented with filling them with different mixtures of gases to create different effects.
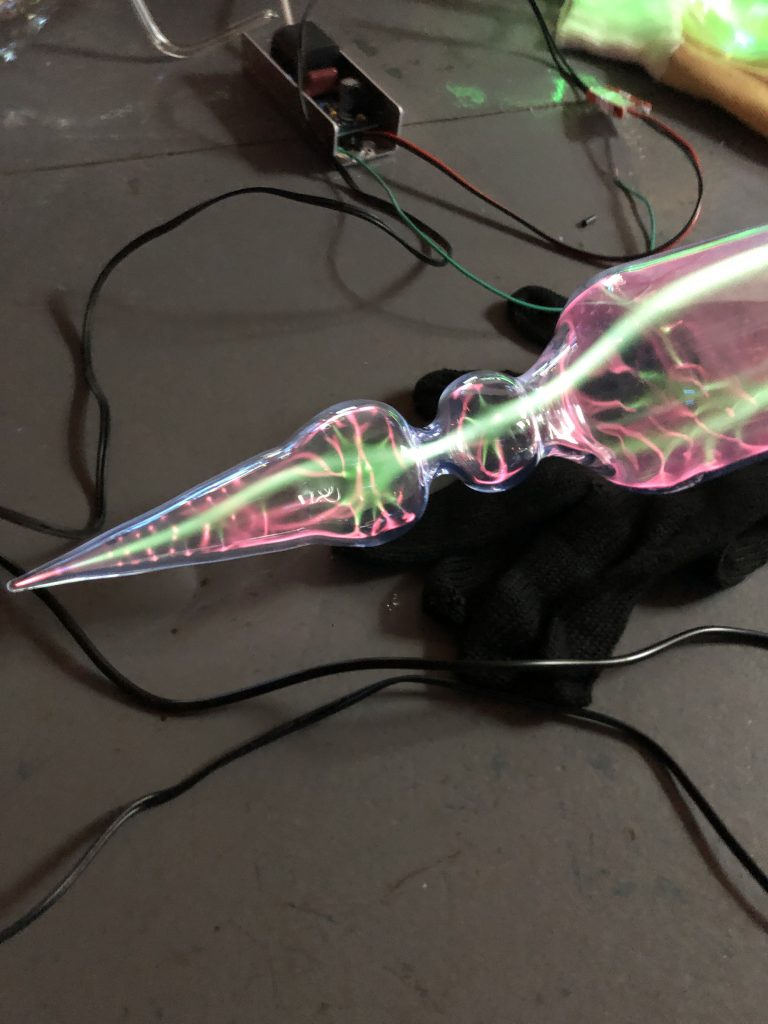
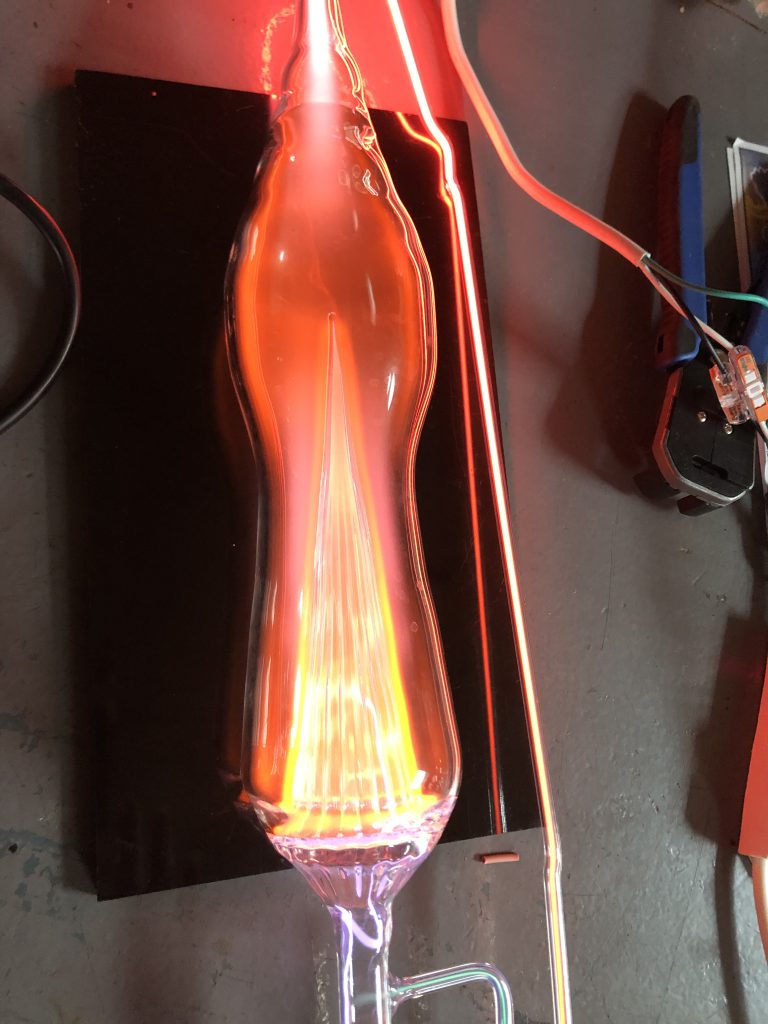
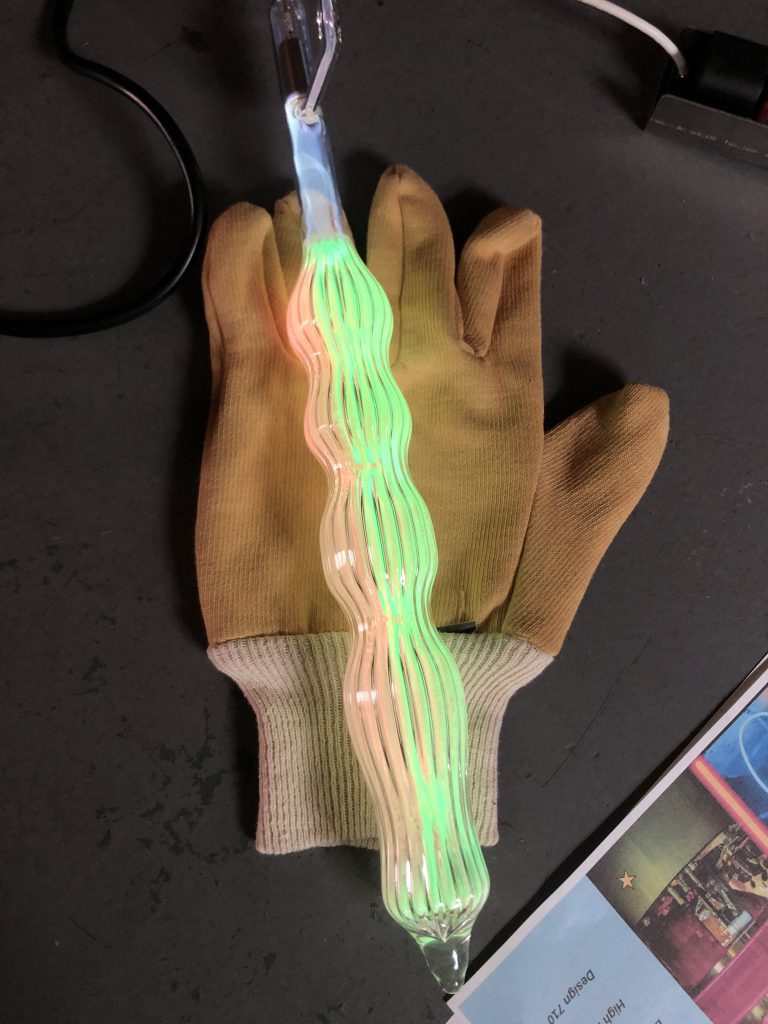
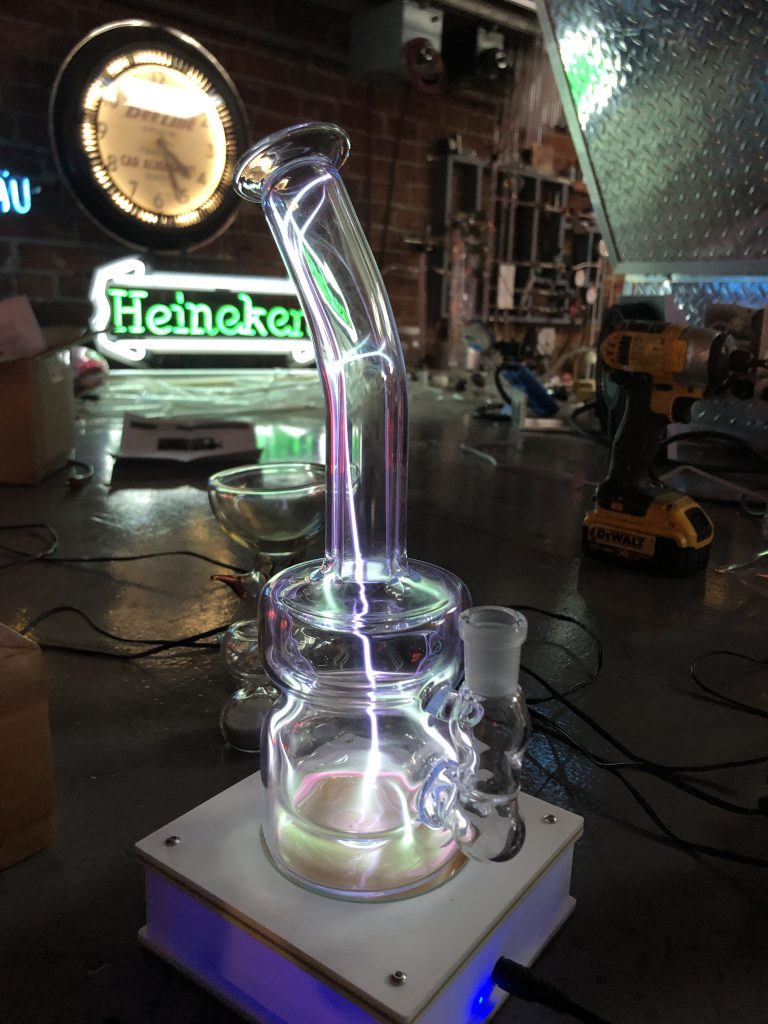
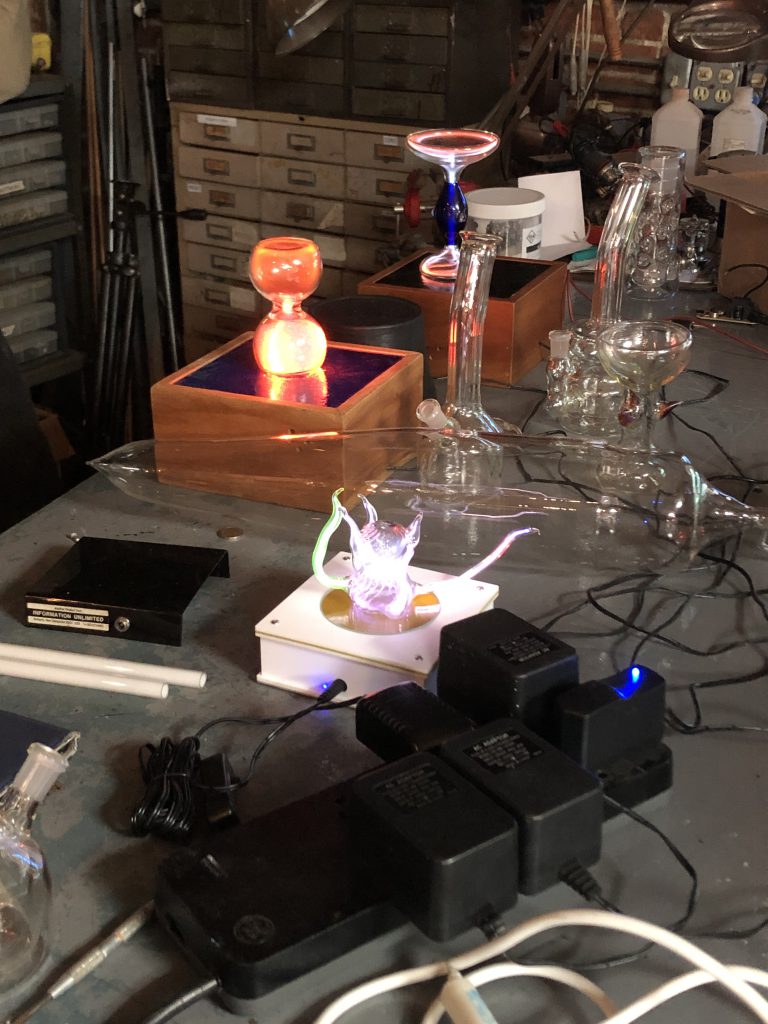
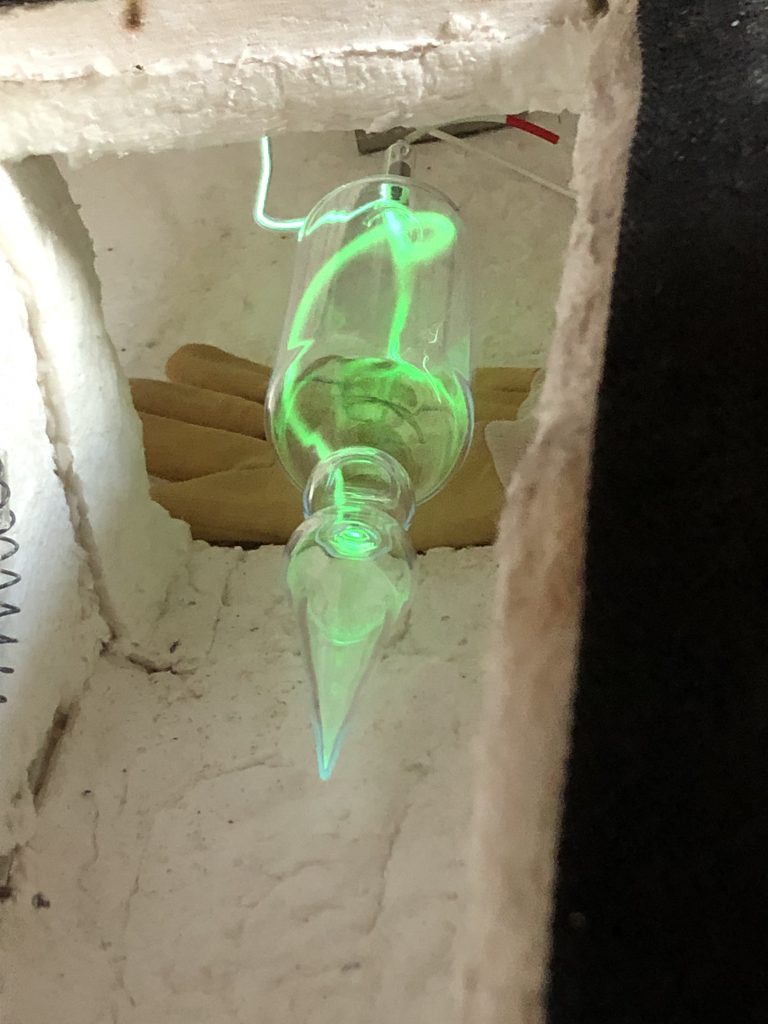
One of the differences between my work making neon lights and what we did at the plasma workshop is that we worked with a different type of glass. Most plasma work uses borosilicate glass (in contrast to the “soft” glass in neon work) which requires a different style of torches that use oxygen in the mix, which produces a hotter flame. Since borosilicate glass has a hotter melting point, it isn’t compatible with neon glass tubing.
Here is a photo of Miles showing us how to tell if two different types are compatible.
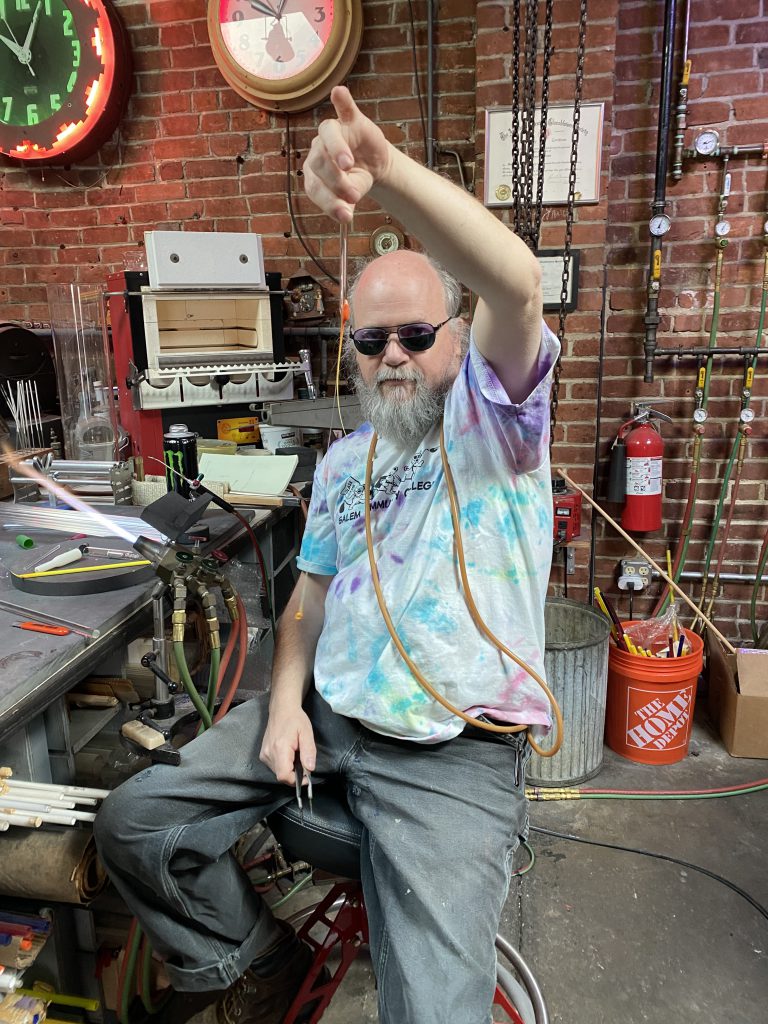
In addition to a different style of torch, borosilicate glasswork often uses a lathe. A glass lathe is a motor-driven machine that allows you to heat the glass as it rotates. Below is a photo of Miles working at the glass lathe.
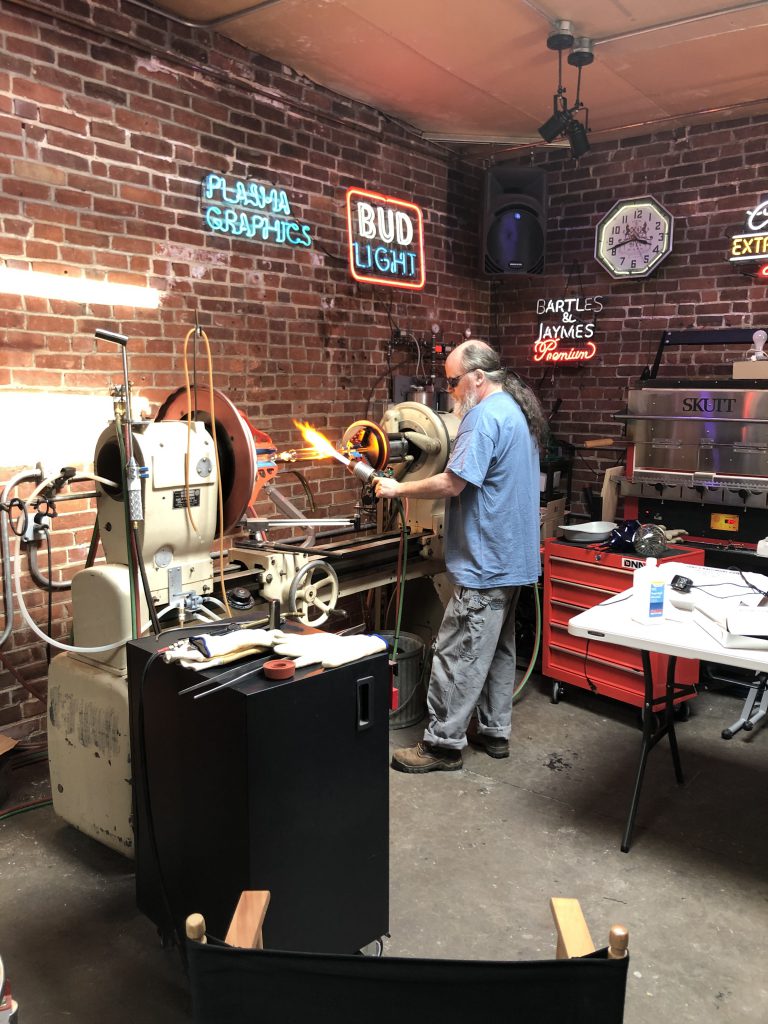
Another difference between making a neon light and the tubes we created in the workshop was the use of an oven to heat up the pieces, rather than the large bombarding transformer used in neon tube production. Here is a picture of the oven that Tom built for his studio at Plasma Graphics.
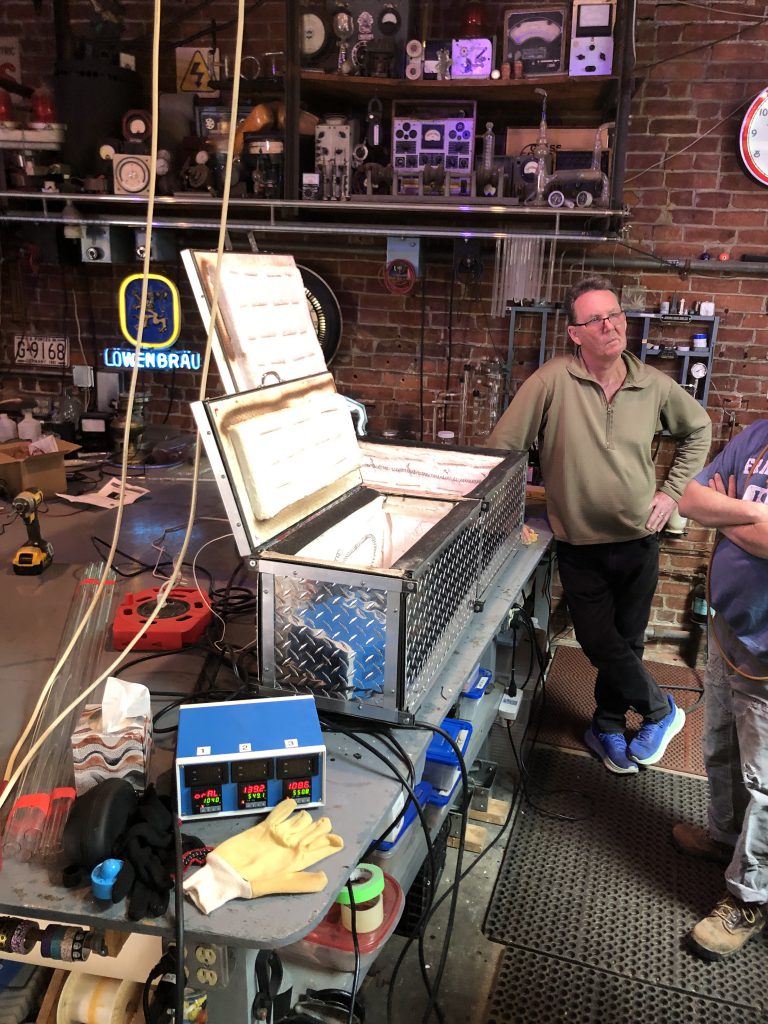
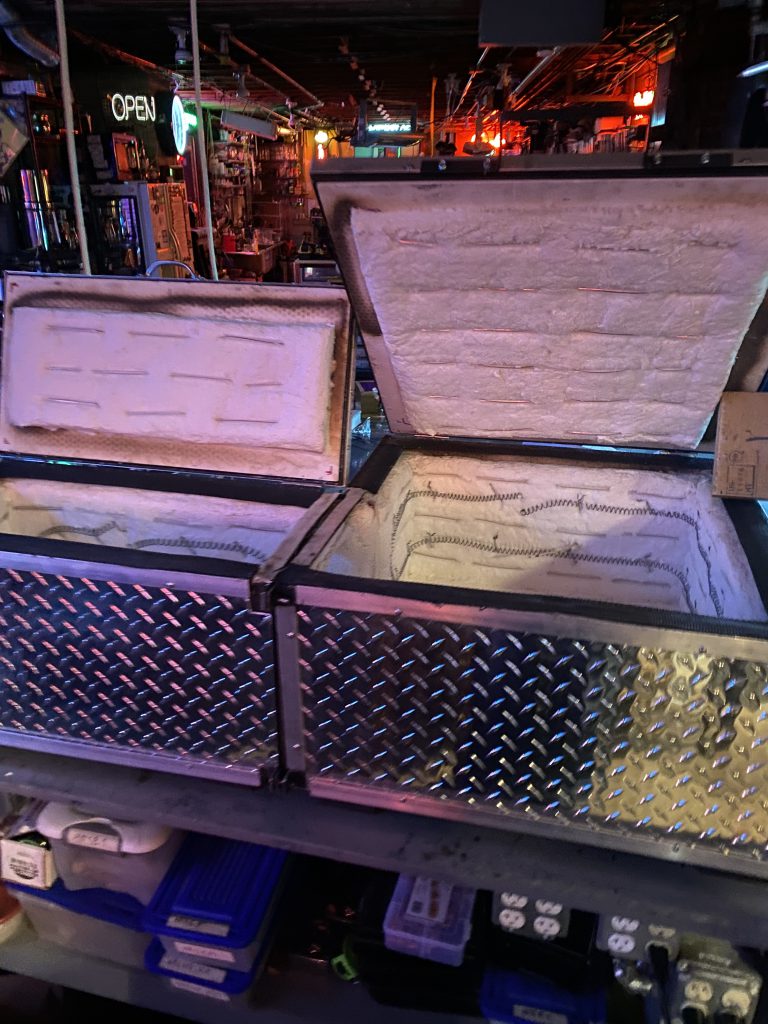
Tom’s processing system included argon and neon gas (as is common in neon sign work) but it also included krypton and xenon gases, which are typical for use in plasma artworks.
Helping with the workshop was long time neon bender, author, and all around wellspring of knowledge and helper to the neon community, Morgan Crook. Here he is showing us how to add colored glass frit to soft glass tubing in the ribbon burner.
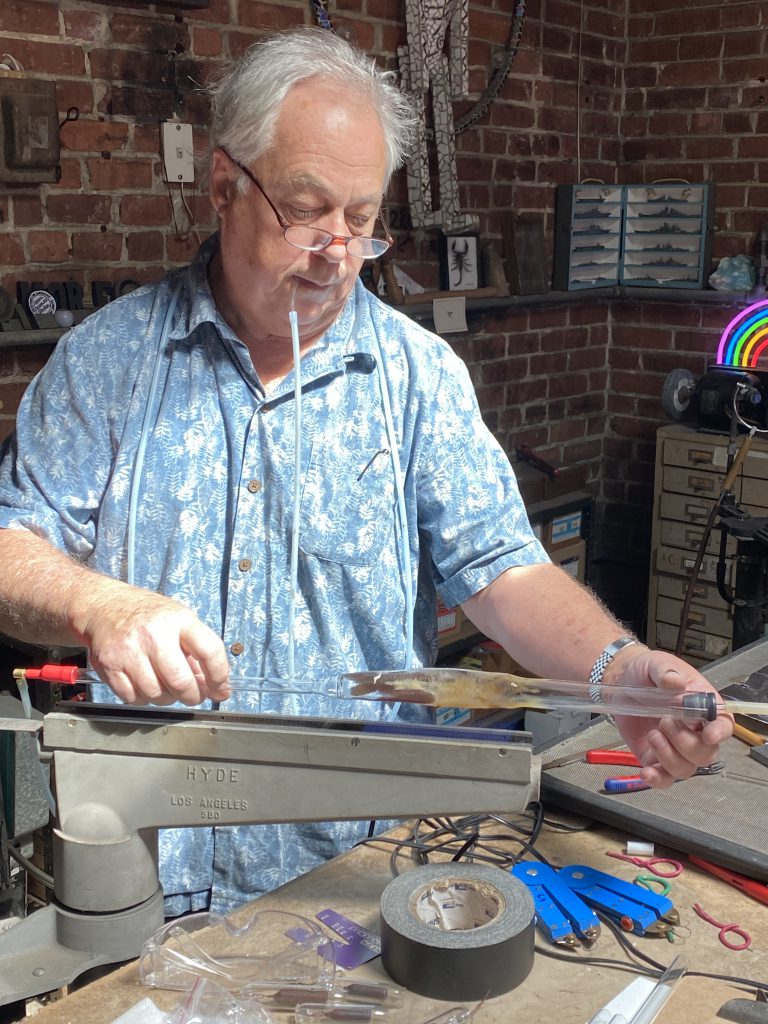
I was having so much fun during the workshop, I didn’t take as many photos as I would have liked to document the experience, but here are a few random ones that I did take.

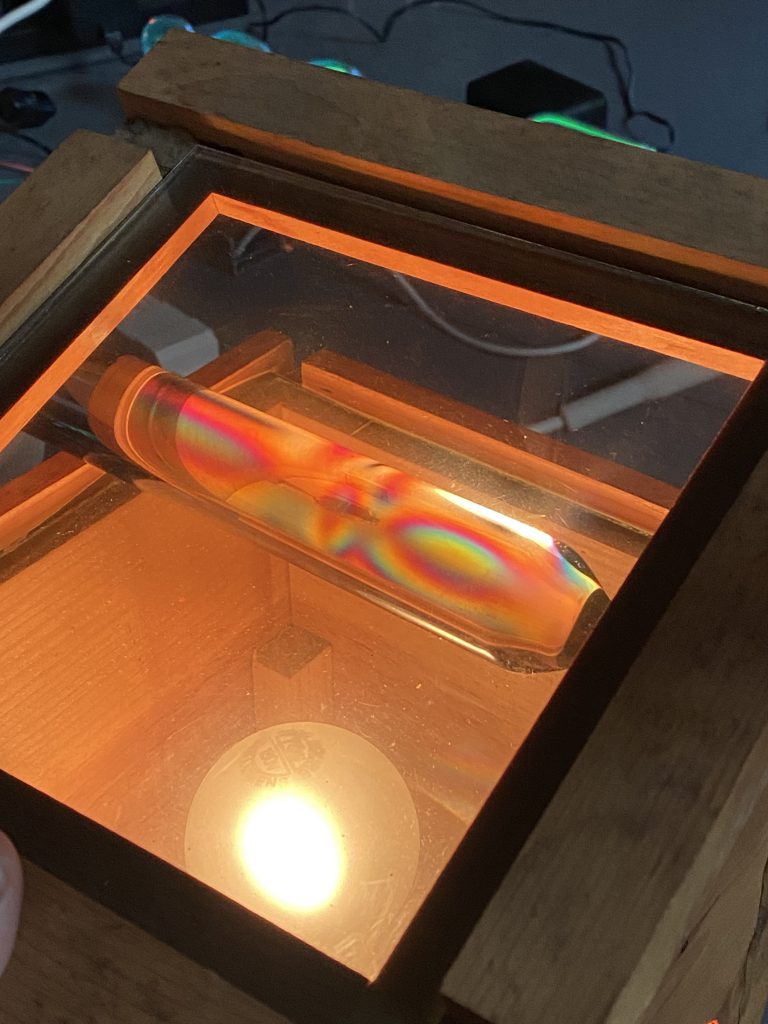
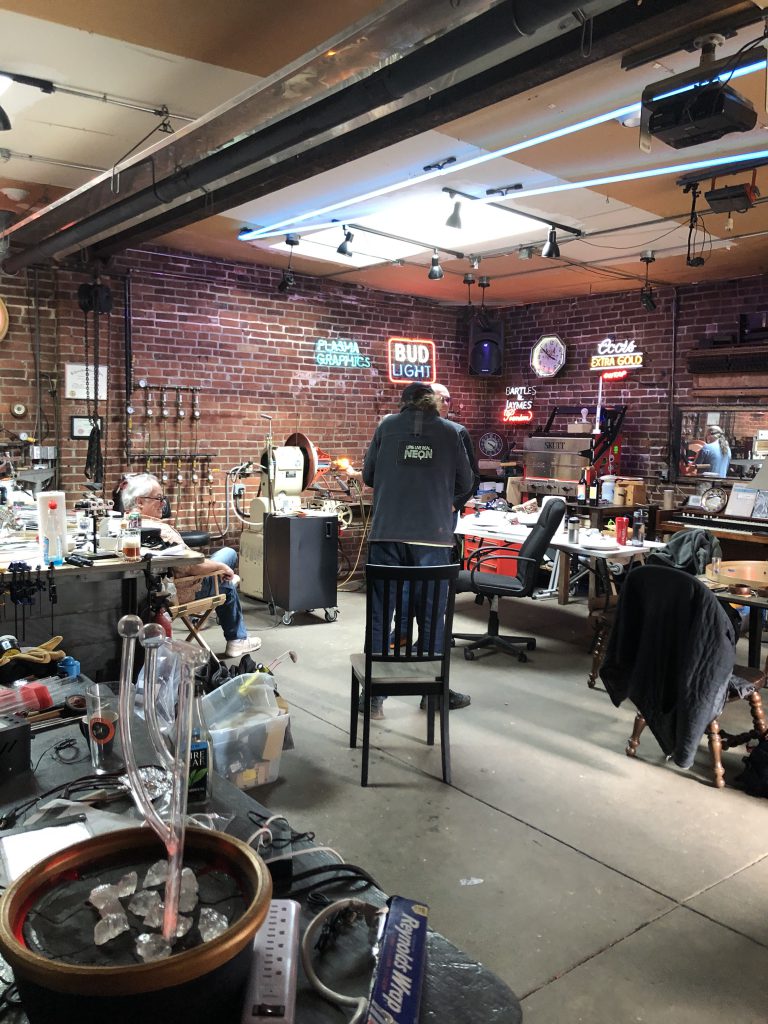
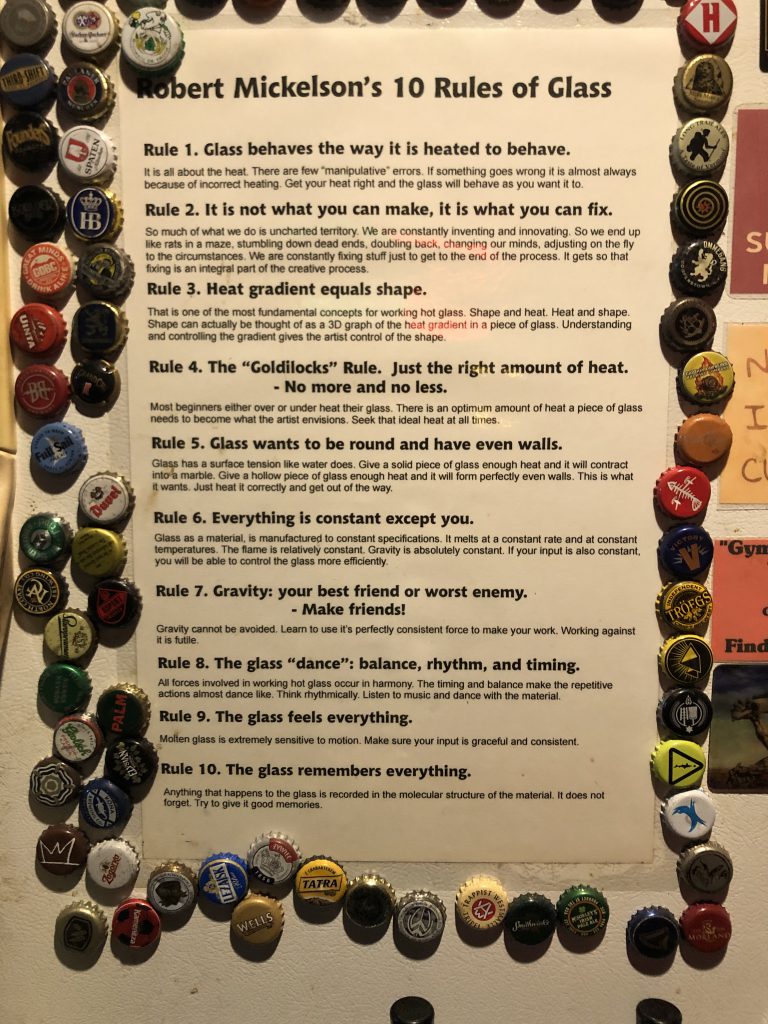
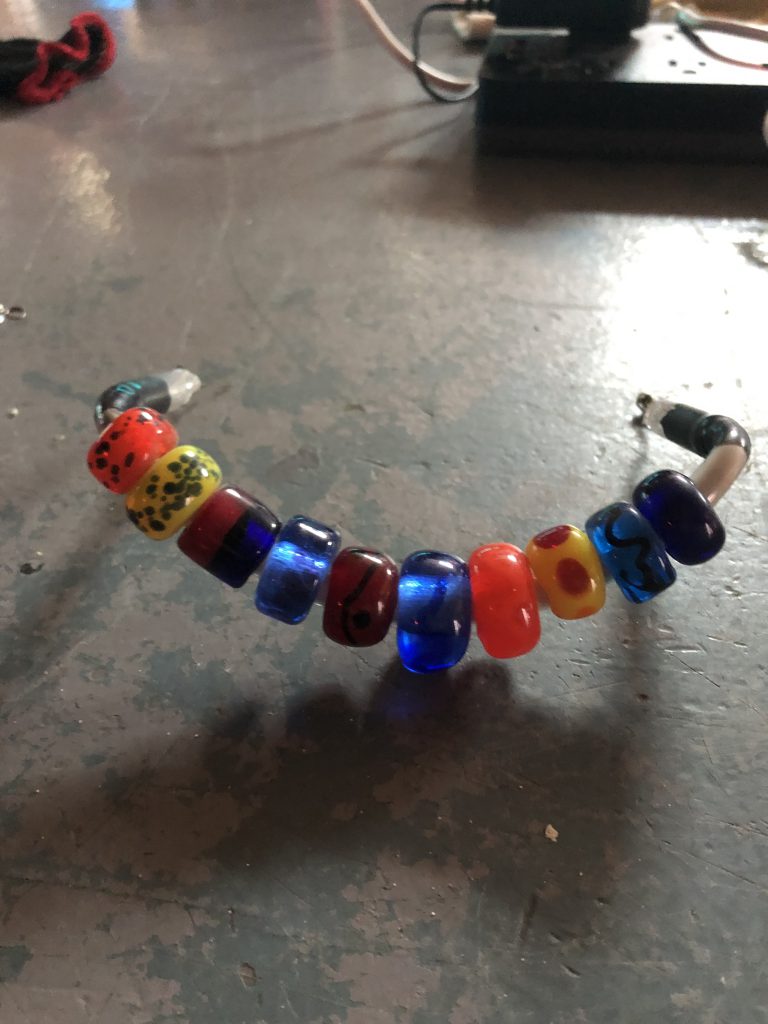
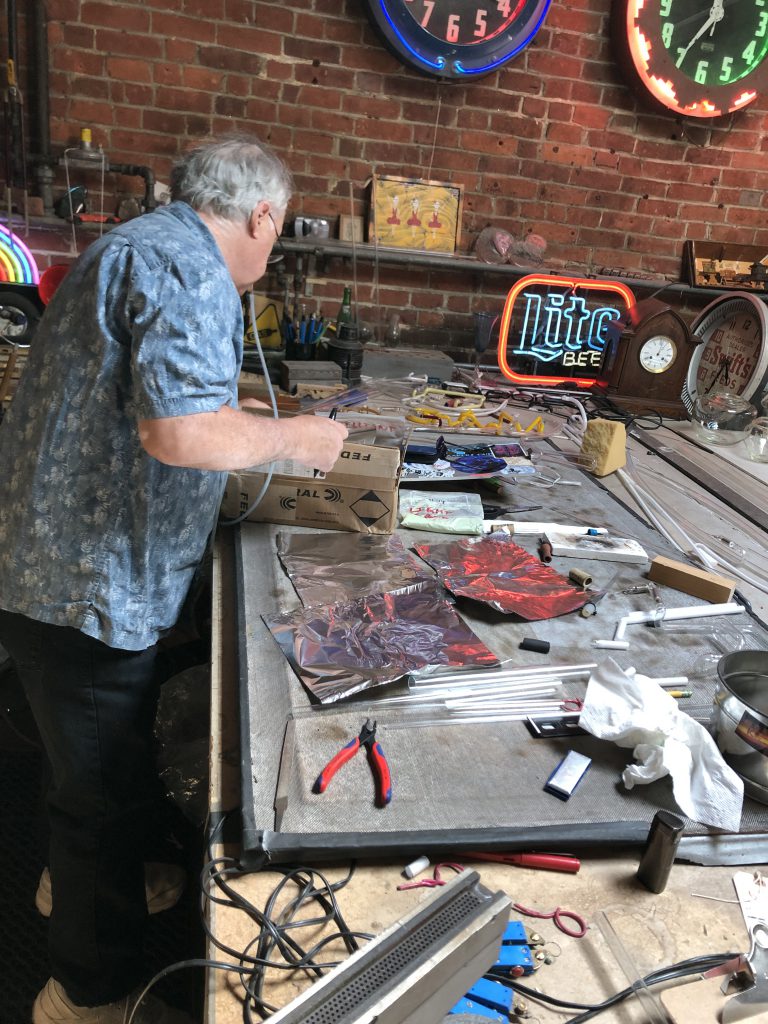
The fun didn’t only happen in the plasma studio though. We had great conversations over dinner and relaxing in between sessions. Two other students in the class I know from previous gatherings of the neon community, and it was great to spend more time with them. And being in Atlantic City, we had to take a walk down to the boardwalk and beach.
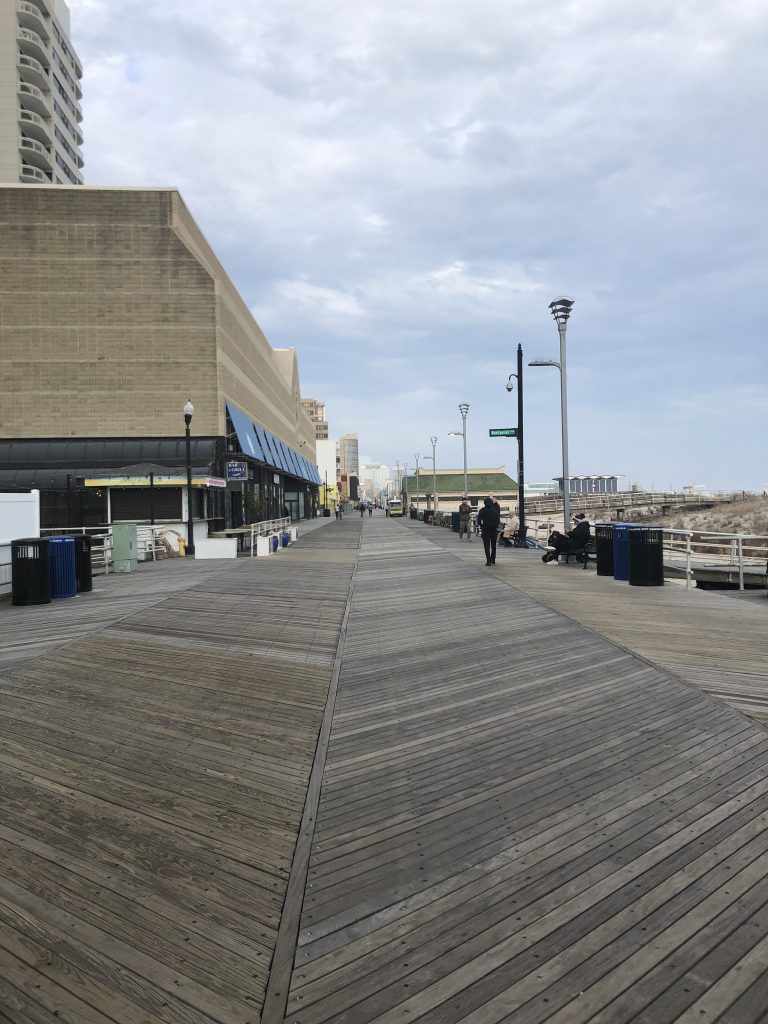
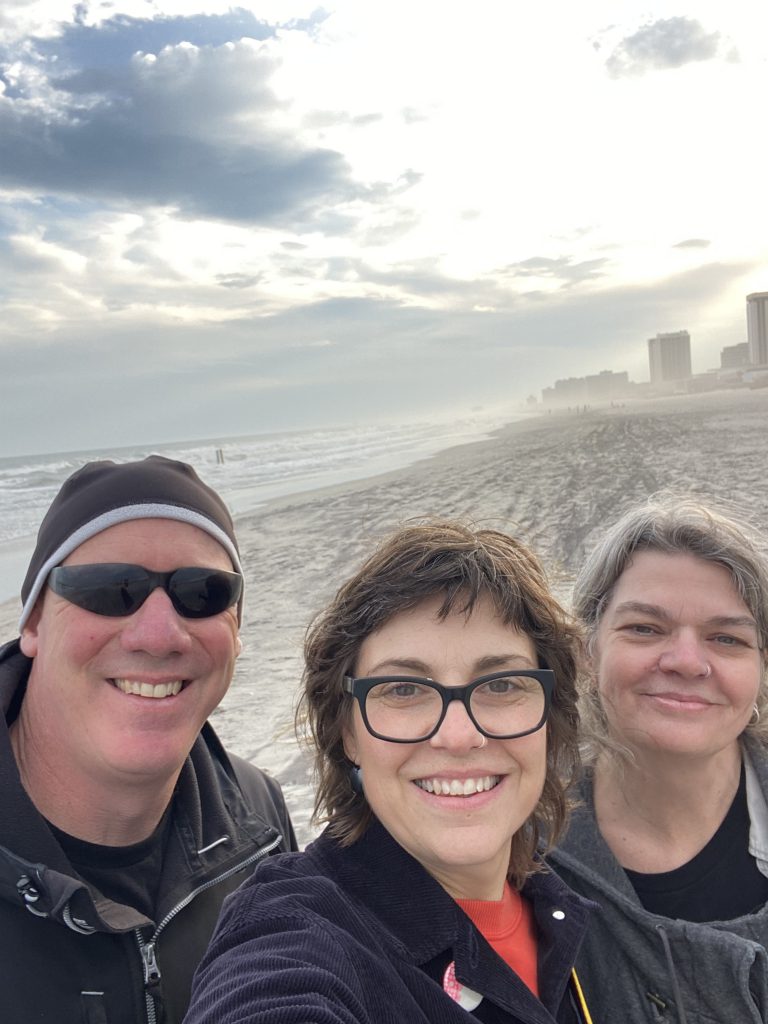
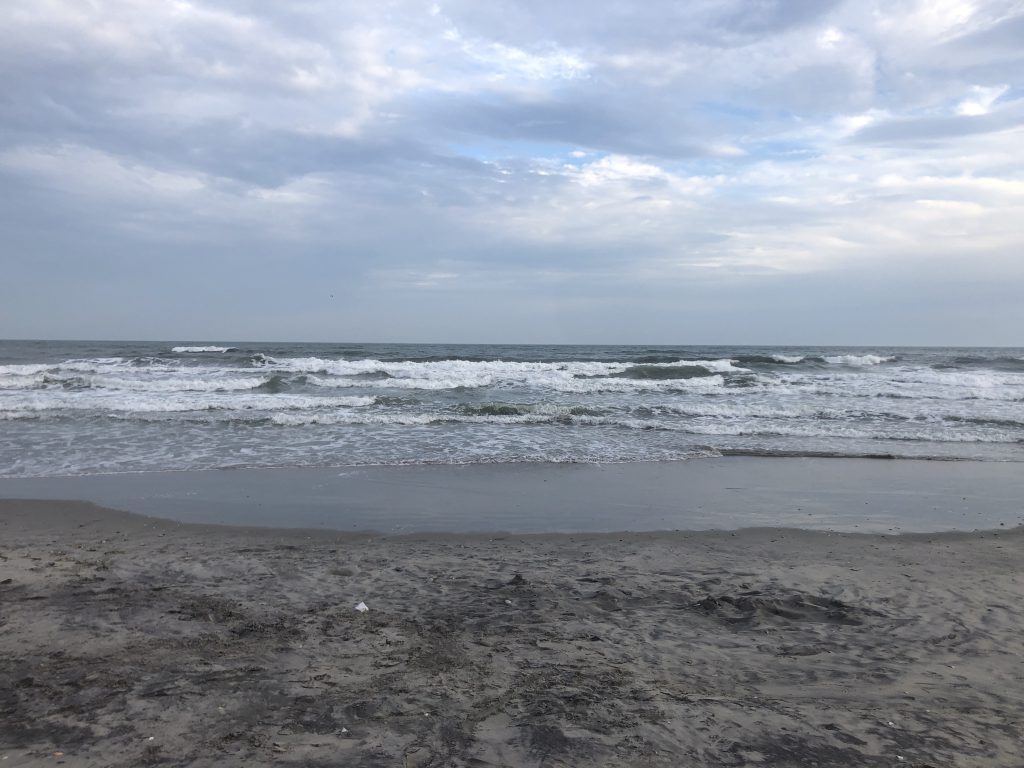
I came away from this experience feeling happy, inspired, and grateful for the opportunity. I’m looking forward to continuing to expand my knowledge and skill set for working with hot glass and nobel gases.
0 Comments